| Step into the fascinating world of textile machinery, where innovation meets tradition to craft the fabrics that shape our lives. This article explores the intricate processes and cutting-edge technologies that have revolutionised textile production, ushering in a new era of efficiency and quality.
Dr Poonam Bhagchandani, Associate Professor, Art & Design, SSDAP, Sharda University
Shivani Chandra, Assistant Professor, Art & Design, SSDAP, Sharda University
New industrial procedures were introduced during the Industrial Revolution, which lasted from the 1760s through some point between 1820 and 1840. As a result of this transformation, new chemical manufacturing processes, automated production methods and iron production were implemented. The Industrial Revolution was primarily driven by the textile industry. The textile business uses varied machines to stitch fabrics and create clothing, carpets and other textile products. These sewing machines, which range in size from enormous heavyduty industrial machines to tiny consumer-sized machines, are employed by individuals for their projects, in factories and only by insignificant textile manufacturers.
Machines involving fibre/yarn/thread production
• Thread winding machines: The fundamental purpose of winding is to move the yarn from one appropriate container to another. Winding is also required for packing, clearing and checking the yarn to enhance quality and eliminate flaws. The purpose of these devices is to wind thread onto spools.
Shivani Chandra,
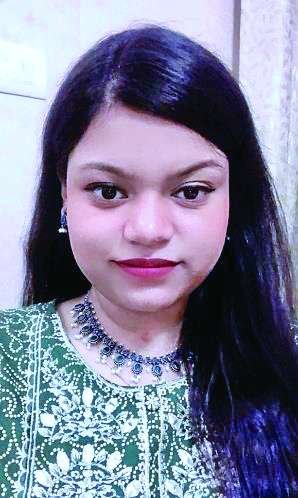
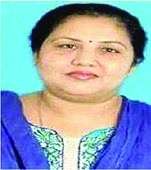
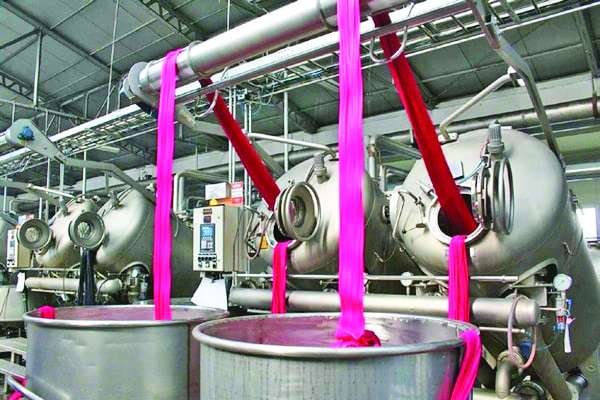
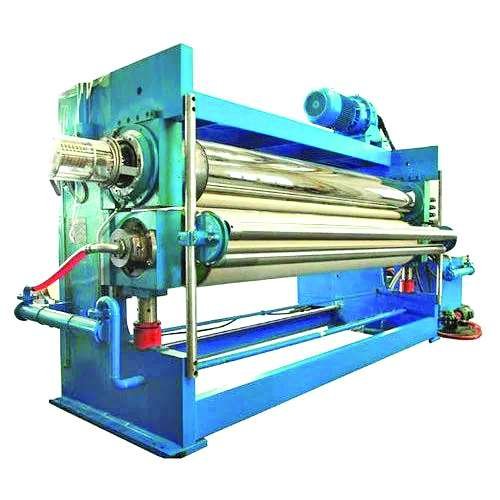
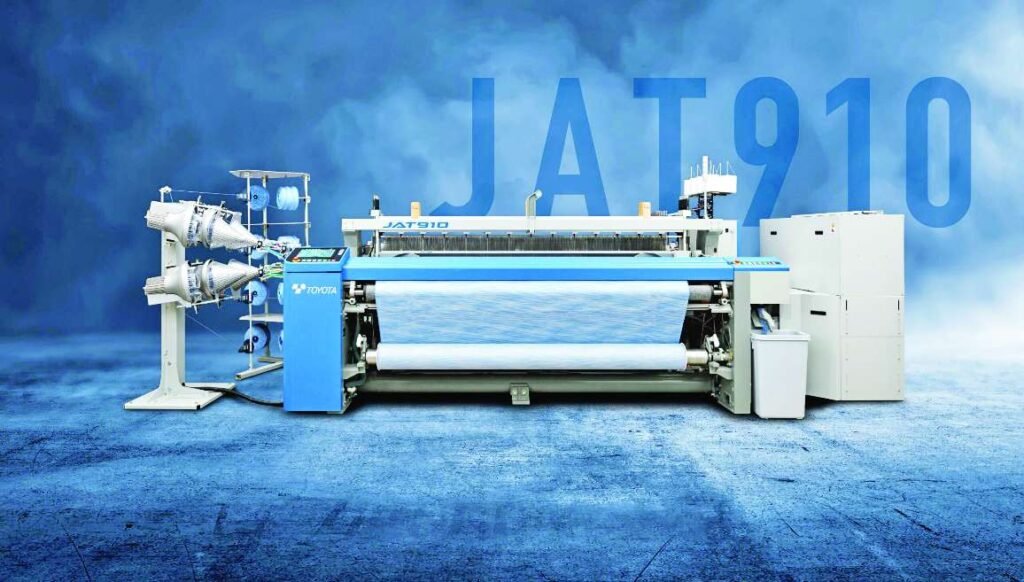
• Spinning machines: Before a thread can be stitched together, it must first be created through the process of spinning. These spinning machines are used to spin materials like cotton into a thread or yarn. The thread or yarn can be knitted or woven together to make a piece of cloth.
• Carding machines: Since carding performs all of the primary duties, it is sometimes referred to as the beating heart of spinning. The dust and grime are removed here after the fibres have been opened up to more or less single strands.
• Bleaching/dyeing machines: One of the most crucial components in the textile business is dyeing. Different forms of cloth colouring are carried out in the dyeing area according to the buyer’s demands and specifications. To provide an even shade with a fastness suited and performance to its end usage, the dyeing procedure is utilised. In contrast, bleaching is used to take out pigments and natural colours that are present in the. It is a chemical process used to remove the substrate’s natural coloration, which can be used on yarn, knitted fabric and woven fabrics.
Textile machinery Some of the major machines that are used in textile manufacturing are:
• Air jet loom machines: Air jet weaving machines are one type of contemporary weaving equipment with the highest weft insertion performance and are thought to be the most productive in the production of light to medium-weight fabrics, preferably made of cotton and certain synthetic fibres (sheets, shirting fabrics, linings, taffetas and satins in staple yarns of synthetic fibres); it must be noted, however, that technically positive results are currently also obtained with heavy weight fabrics (denim, leather etc.). For individuals who wish to make large numbers of bespoke fabric styles, these machines are the best option. Generally speaking, the weaving widths range from 190 to 400 cm. There are up to eight distinct colours on the multi-colour weft carrier. The JAT910 AIR JET LOOM (Fig 1) by Toyota has embraced the goal to continue growing with its consumers while understanding their changing demands.
• Air jet spinning machines: Contra-rotating twin jets are used in Murata’s Vortex Jet Spinning (MJS) to improve the wrapping of edge fibres. The research has demonstrated that the cross-sectional number of fibres affects jet spinning. Given that the number of wrapper fibres is capped by the number of edge fibres on the surface and that the strength is directly correlated with the wrapper fibres. When the yarn’s fibre count rises, the proportion of wrapper fibres decreases and the tenacity drops. Additionally, the wrapping length decreases with increasing count coarseness, which lowers tenacity. As a result, two difficulties required attention: a greater quantity of wrapper fibres and a longer extent of wrapper fibres. The Murata Vortex Spinning (MVS) technology resolves some of the problems with prior iterations of air-jet spinning systems by using more than two air jets to form a 3D air vortex. By producing more edge fibres, switching from a 2D to a 3D system enables a considerable increase in the number of wrapper fibres.
• Fabric finishing machine The Automatic Textile Calendaring Machine (Fig 2) has attached rollers that guarantee crease-free travel. The machine’s top advantages include trouble-free operation, smooth performance and low maintenance requirements. They have designed models specifically to meet the needs of the textile industry, providing dimensional stability to all types of materials. As implied by the name, calendaring is the process of treating cotton with a strong caustic alkaline solution to enhance its shine, stability, tensile strength, water sorption and other qualities. For all wholesale orders, this machine is provided to the clients at prices that are at the top of the market.
• Jet dyeing machine India’s Surat-based Apex Engineers (Fig 3), the most advanced machine for dispersing colouring polyester fabric is the jet dyeing machine. These machines allow for a speedier and more consistent dying process because the cloth and dye fluid are both in motion. There is no fabric driving reel to move the cloth in a jet dyeing machine. The force of the water helps the cloth move. It is affordable because of the low alcohol percentage. In contrast to a long tube dyeing machine, only four valves are needed to regulate the movement of the cloth, making it more user-friendly. There is only one valve in jet dyeing equipment and fabric dyeing machines.
Conclusion
These are some of the highly automated, effective machines that are now utilised in the textile manufacturing sectors and that will also alter the course of production in the future. The textile industry is not only evolving but also revolutionising itself. It is on the cusp of a new era, promising textiles that are not just functional but also environmentally conscious. With each advancement, the fabric of our future becomes brighter and more technologically advanced than ever before.