| Die and mould are responsible for shaping plastic material to the desired design and shape of the toy. They ensure that the toy is manufactured in large quantities with consistency and precision. A read on…
Gaurav Mirchandani,
Founder & CEO,
SM Toys
The die and mould industry plays a crucial role in the manufacturing of toys in India. Die and moulds are specialised tools used in the production of toys, allowing manufacturers to create toys with consistent shapes, sizes, and intricate details.
Most of the items for sale in toy aisles across the nation are made of plastic, as can be seen by taking a stroll down any one of them. Many of them have probably been produced using techniques for plastic injection moulding. Building blocks, dolls, robots, and craft kits are just a few of the toys and games that can be produced using plastic injection moulding to appeal to kids.
Manufacturing processes
Die and mould are used in the injection moulding process, which is one of the most common manufacturing processes in toy production. In this process, the plastic material, usually referred to as thermoplastic, is heated and melted in the injection moulding machine. The melted plastic is then injected into a die that is formed to shape the plastic into the desired design of the toy. After cooling down, the plastic toy is then released from the mould.
Die-casting is a popular method of mass production in metal processing. Molten metal is frequently injected under high pressure into a steel mould cavity, where it solidifies into its final shape. The steel mould is made up of at least two portions that can be separated to release the cast result. In many ways, die-casting is like plastic injection moulding. Due to the steel construction of the injection system and die (mould), the bulk of die-cast items are made of metals with lower melting points, such as zinc, copper, aluminium, magnesium, lead, and their alloys.
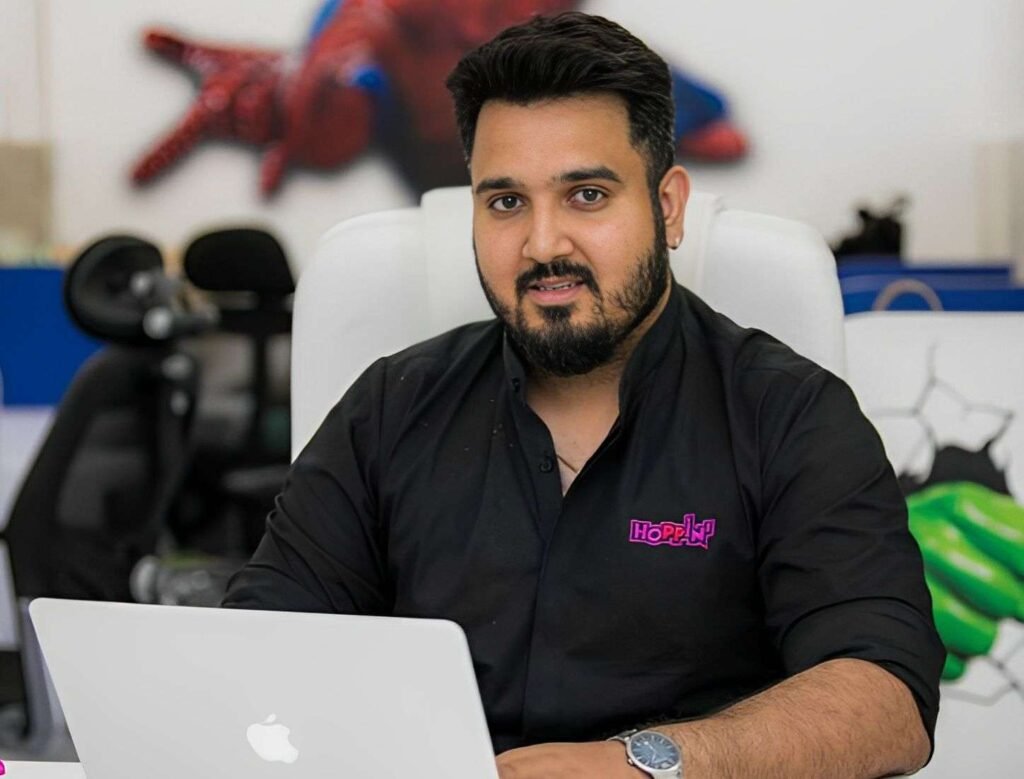
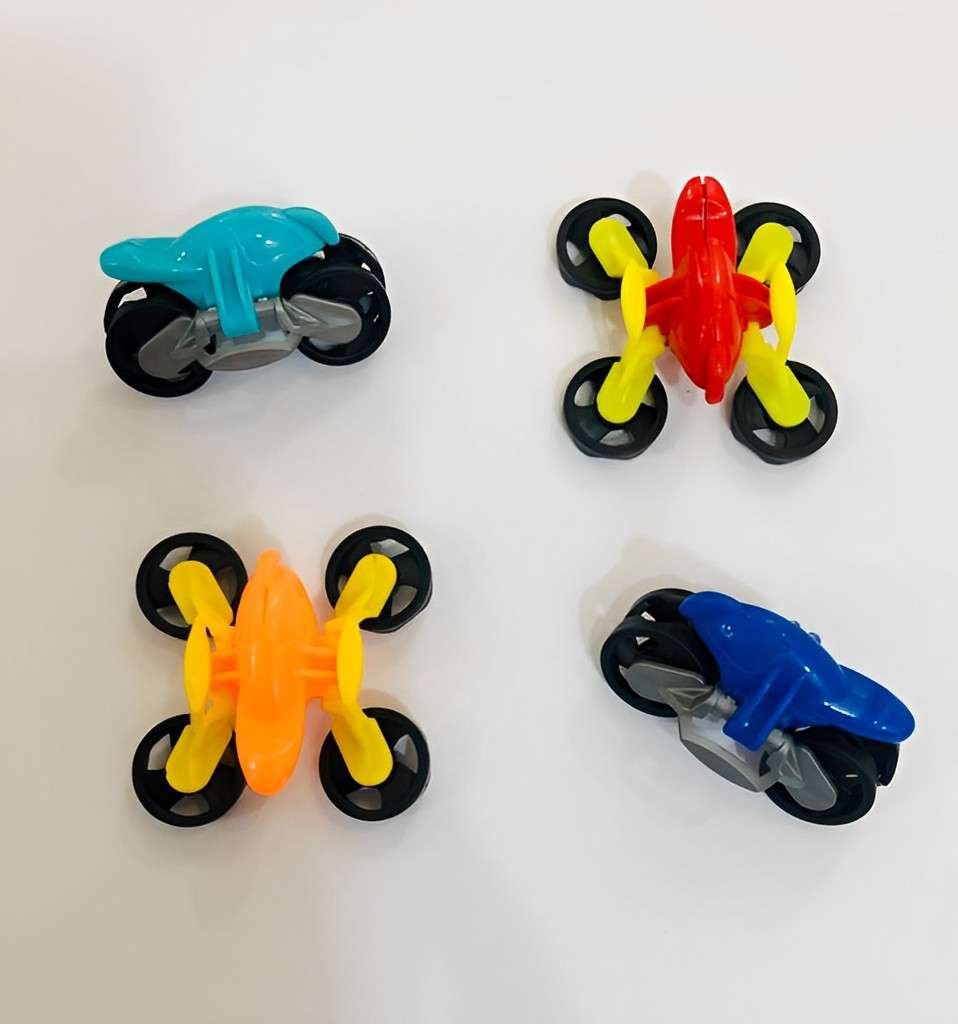
Going back in time
The creation of die-cast toys began in the early twentieth century. The bulk of die-cast toys are constructed of zamak, a zinc alloy with trace quantities of aluminium and copper. When compared to wood, plastic, and sheet steel, one appealing characteristic of die-cast toy manufacture is the capacity to make extremely detailed, precision models. Die-cast toys are more durable than hollow-structure toys made of steel sheets or plastic, regardless of the level of detail and precision.
Blow moulds are used to produce hollow plastic toys, such as bottles, balls, and inflatable toys. In blow moulding, plastic is melted and formed into a hollow tube, which is then inflated inside a mould cavity to take the shape of the mould. The plastic then cools and solidifies, and the toy is ejected from the mould. Blow moulds are typically made of steel or aluminium and are designed with the desired shape and size of the toy.
Rotational moulds, also known as roto moulds, are used to produce large plastic toys, such as playground equipment, ride-on toys, and outdoor furniture. In rotational moulding, the plastic powder is placed inside a mould, which is then heated and rotated in multiple axes to evenly coat the interior of the mould with melted plastic. The plastic then cools and solidifies, and the toy is ejected from the mould. Rotational moulds are typically made of aluminium or steel and are designed with the desired shape and thickness of the toy.
Defining die and mould in toy manufacturing
Here are some key aspects of the role of die and mould in toy manufacturing in India:
1. Toy Design and Development: Die and moulds are used in the design and development stages of toy manufacturing in India. Toy designers and engineers create prototypes and models of toys using specialised die and moulds. These tools help in creating accurate and precise toy parts, ensuring that the final product meets the desired design specifications..
2. Mass Production: Once the toy design is finalised, die and moulds are used in the mass production stage of toy manufacturing. These tools enable manufacturers to produce toys in large quantities with consistent quality and precision. Die and moulds are used to create various toy components, such as body parts, accessories, and small details like eyes, noses, and mouths, which are then assembled to create the final toy product.
3. Cost-Effective Production: Die and moulds help toy manufacturers in India achieve cost-effective production. Once the initial investment is made in creating the dies and moulds, they can be used repeatedly to produce a large number of toys. This helps reduce the per-unit production cost and increase overall profitability for toy manufacturers.
4. Customisation and Innovation: Die and moulds also enable toy manufacturers in India to customise and innovate their toy designs. Customised die and moulds can be created to produce toys with unique shapes, sizes, and features, allowing manufacturers to cater to specific customer preferences and market demands. Die and moulds also facilitate innovation in toy design by enabling manufacturers to create new and unique toy concepts.
5. Quality and Safety: Die and moulds play a crucial role in ensuring the quality and safety of toys. Accurate and precise die and moulds help produce toys with consistent quality and safety features. For example, die and moulds are used to create parts with smooth edges, preventing sharp edges that could potentially harm children. Die and mould production also aid in producing toys that comply with safety regulations and standards set by various national and international agencies.
6. Export and Global Competitiveness: The role of die and moulds in toy manufacturing in India is also crucial for exports and global competitiveness. With high-quality die and moulds, Indian toy manufacturers can produce toys that meet global standards, enabling them to compete in international markets. Die and moulds help Indian toy manufacturers produce toys efficiently and cost-effectively, making them competitive in the global toy market.
Contributing to the toy manufacturing ecosystem
In conclusion, die and moulds play a vital role in the manufacturing of toys in India. They are used in various stages of toy production, including design, development, mass production, customization, and innovation. Die and moulds enable cost-effective production, ensure quality and safety, and help Indian toy manufacturers compete in the global market. The die and mould industry in India is a critical component of the toy manufacturing ecosystem, driving innovation, efficiency, and competitiveness in the industry