| The Aerospace and Defence sector holds utmost significance in any nation. This article emphasizes how automation, technologies such as Artificial Intelligence (AI), Big Data, and simulation tools can enhance this vital industry.
Sunil Dixit, Country Manager, India, Markforged
In the dynamic realm of aerospace and defence, where precision, reliability and innovation reign supreme, the convergence of cutting-edge technologies is redefining the landscape. Among these technologies, 3D printing stands tall as a transformative force, revolutionising how complex components are created. However, the true potential of 3D printing is unleashed when it is coupled with AI, data analytics and simulation, a triad that is propelling these industries into a new era of efficiency and adaptability.
Evolution of 3D Printing
The journey of 3D printing from being a mere novelty item creator to a powerful tool for crafting intricate aerospace and defence components has been nothing short of remarkable. With the advent of Industry 4.0 and the digitisation of manufacturing processes, 3D printing has transformed into a data-driven phenomenon. This transformation has empowered 3D printers to gather extensive information about the fabrication process, creating a wealth of data that becomes the bedrock for further innovation.
Data-driven 3D Printing
At the heart of data-driven 3D printing lies the immense treasure trove of information that is collected during the fabrication process. Smart 3D printers, interlinked with digital repositories of existing components, possess the capability to discern the ideal candidates for additive manufacturing techniques. By analysing historical data and patterns, these printers can not only optimise the manufacturing process but also predict potential pitfalls.
In the aerospace and defence industry, where precision and reliability are non-negotiable, the ability to ensure the quality of each printed component is paramount. AI algorithms, fed with the wealth of data gathered during the fabrication process, become vigilant sentinels. They meticulously inspect components as they materialise, identifying anomalies and ensuring the highest standards of quality. The synergy of data and AI not only expedites production but also serves as an insurance against faulty parts, contributing to the industry’s uncompromising safety standards.
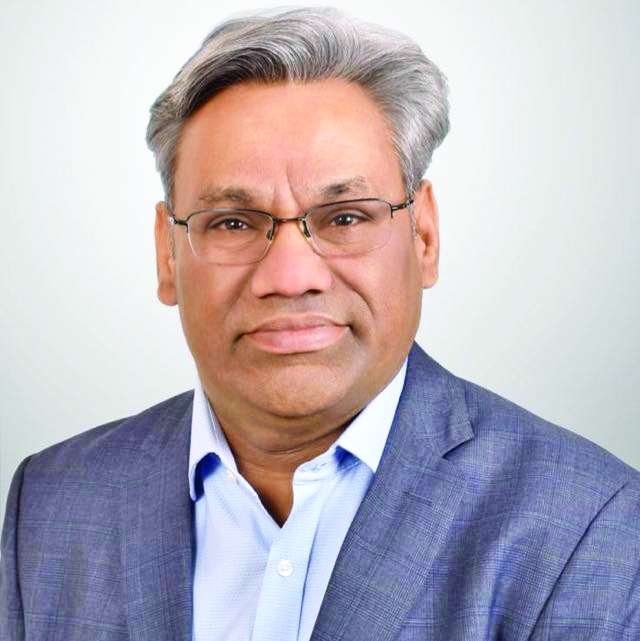
Sunil Dixit
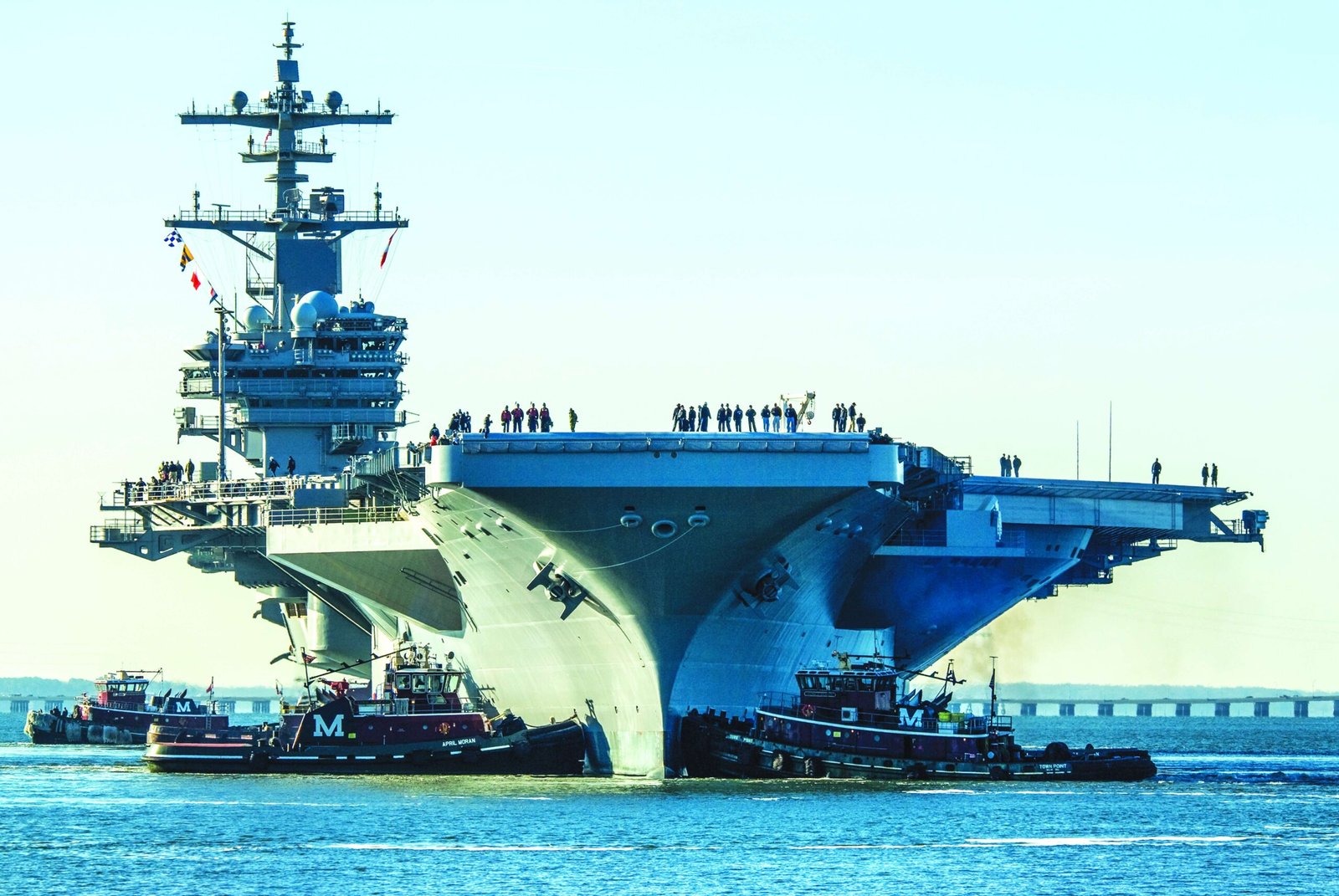
AI, Data and simulation in Aerospace and Defence
AI’s empowering effect on 3D Printing
Artificial intelligence (AI) adds a layer of intelligence to 3D printing that extends beyond quality assurance. It empowers 3D printers to make autonomous decisions, optimising the manufacturing process for performance, cost and time constraints. These AI-driven decisions are not merely reactive but proactive, adapting to real-time challenges and dynamically adjusting printing parameters to ensure optimal outcomes.
Furthermore, AI’s prowess reaches beyond the fabrication process. It assists engineers in the design phase by simulating and optimising the structural integrity of the components. Complex aerospace and defence parts often need to withstand extreme conditions, and AI-powered simulations play a pivotal role in predicting how these parts will perform under stress. By mimicking real-world scenarios, these simulations enable engineers to fine-tune designs for maximum efficiency, durability and safety.
Simulation: In innovation
Simulation is the bridge that connects data and AI in the realm of 3D printing. It enables engineers and designers to virtually test their creations in a controlled environment, making informed decisions before physical production even begins. In the aerospace and defence industry, where precision and reliability are typically tested over and over through multiple, varied iterations, simulation is a game-changer.
In the context of composite materials, which play a crucial role in aerospace and defence applications due to their lightweight and durable nature, simulation is particularly impactful. It allows designers to experiment with various composite material combinations, structures and manufacturing methods, predicting how these variations will affect performance under different conditions. By optimising the design through simulation, engineers can avoid costly iterations and streamline the path from concept to reality.
Benefits for aerospace and defence
The amalgamation of AI, data analytics and simulation catapults 3D printing to new heights in the aerospace and defence industries. The ability to predict and prevent defects through data analysis, coupled with AI-driven decision-making, minimises risks and ensures consistency in production. Simulation, on the contrary, paves the way for innovation, allowing designers to push the boundaries of what’s possible, maintaining rigorous quality standards.
For aerospace and defence supply chains, notorious for their vulnerability to disruptions, this triad of technologies presents a silver lining. The real-time data acquisition and analysis ensure that supply chains can swiftly adapt to unforeseen disruptions, offering a buffer against the unpredictability that often plagues these industries. With the capability to simulate and optimise designs, engineers can accelerate the development of new components and adapt existing ones to changing requirements, facilitating agile responses to emerging challenges.
Markforged and the futuristic approach
Navigating uncharted skies with confidence, as the aerospace and defence industries continue their relentless pursuit of innovation and efficiency, the role of AI, data and simulation in 3D printing is set to be a cornerstone of progress. The future envisions aerospace and defence manufacturers harnessing the power of AI to make data-informed decisions, while simulation acts as a virtual playground for testing and refining designs.
As this convergence gathers momentum, the aerospace and defence sectors will be well-equipped to navigate the challenges of an ever-evolving landscape, confident in their ability to create, adapt and excel. Through the fusion of AI, data and simulation, 3D printing emerges not just as a manufacturing technique, but as a catalyst for innovation, resilience and progress in the aerospace and defence industries.
Markforged (NYSE:MKFG) is making manufacturing more resilient and flexible by bringing on-demand industrial production to the point of need. The Markforged Digital Forge, a reliable, intelligent and easy-to-use additive manufacturing platform, empowers any manufacturer to create strong and accurate end-use parts repeatedly in both metal and composites anywhere and anytime.
Over 10,000 customers across more than 70 countries use ‘The Digital Forge’ to overcome limitations of traditional manufacturing while strengthening their supply chains. Markforged is headquartered in Waltham, Massachusetts, where it designs the hardware, software and materials that powers its platform.