In an exclusive interview with Kaushanth Dighavkar, Prashanth Alevoor, Managing Director, Dürr India, discusses how Dürr is driving innovation in air ducting, process integration, and sustainable manufacturing. He shares insights on the company’s localisation efforts, advanced automation, and AI-powered solutions that enhance efficiency across industries. Alevoor also highlights Dürr’s commitment to energy savings and environmental sustainability in the evolving manufacturing landscape.
- Can you elaborate on how Dürr’s innovative air ducting system optimises energy usage and enhances safety standards, especially in high-demand industries like automotive and battery production?
Dürr’s innovative air ducting system is not limited to the aircraft painting industry but is also applicable to other sectors, such as automotive. This system proves particularly beneficial in situations where paint booths cannot maintain constant temperatures and humidity levels using recirculated air and must rely on supply and exhaust air instead. This scenario often arises with manually applied paints, where workers are present in the paint booth. Aircraft paint booths, being significantly larger, require substantial energy for conditioning. Dürr addresses this by implementing a component-specific air flow that significantly reduces the required air volume while still meeting safety requirements and standards. Reducing the air that needs conditioning directly lowers the energy consumption. In the automotive sector, painting is typically automated, allowing for recirculation in plant booths. Since no personnel are present in the spray booths, air quality is not an issue. Dürr’s new EcoProBooth exemplifies this efficiency, achieving up to 95 % air recirculation, which reduces both energy consumption and CO2 emissions. However, Dürr’s innovative air ducting system is advantageous in the automotive industry only in cases of manual painting or when pursuing highly sustainable painting processes. This, however, involves substantial investment costs.
- Dürr offers a comprehensive solution through process integration. How does your turnkey approach, from paint extraction to control systems, streamline operations and reduce operational downtime for manufacturers?
This is accomplished through an integrated solution encompassing various facets of the manufacturing process, from planning and implementation to maintenance. At Dürr, we engage from the consulting phase through project completion, enabling us to gain a deep understanding of customer requirements and design tailored processes to meet them. Our turnkey approach integrates Dürr’s innovative products, precision-engineered and manufactured in Germany under controlled conditions, to address multiple aspects of the manufacturing process cohesively. This minimises disruptions, boosts efficiency, and optimises overall operational performance. Our global expertise ensures seamless integration of processes and products, resulting in reduced downtime, high productivity, and enhanced reliability for our customers.
- With a presence in India since 1997, how has Dürr adapted its offerings to meet the unique challenges and demands of the Indian market across different sectors?
Since 1997, Dürr has been deeply entrenched in the Indian market, delivering state-of-the-art paint application and process solutions to a wide range of industries, including passenger and commercial vehicles, two-wheelers, three-wheelers, agricultural and construction machinery, and electric vehicles. This reflects our ability to tailor approaches for each segment. Each customer faces unique operational challenges, in delivering top-notch products to their end consumers, and we add value by helping them achieve their objectives. Our success in India market stems from our strong focus on localisation— over 80% of our operations are localised, including fully localised engineering activities that adhere to global expertise and practices, a feat of which we are incredibly proud. Our technological innovations and customised solutions enable us to address the diverse and complex issues prevalent in the Indian market. We benefit from a vast knowledge base within our global group and maintain close proximity to our customers through strategically located offices, ensuring exceptional service support.
- Dürr serves a wide range of industries, from automotive to pharmaceutical. How does your team approach the unique demands of each sector, and what role does technology play in ensuring flexibility?
Dürr operates across diverse industries, offering innovative and tailored solutions. This is achieved through global engineering teams with extensive experience in various sectors. New employees undergo specialised training in these segments. In addition, a close contact with our customers is crucial for understanding their needs and where the journey should take them in the future. For instance, in industrial products, Dürr has observed increasing demand for automated painting processes. To address this, we focus on our ready2integrate technologies which align individual products into high-quality solution. These solutions include a controller, dosing technology, and applicator, combining to improve ramp-up time, reduce project risks, and simplify integration. An integrator customises these selected products at the customer’s site, resulting in systems tailored to each customer’s individual painting process.
- How does Dürr’s Clean Technology Systems division assist clients in meeting stringent environmental and emission standards, especially with products like air pollution control and noise abatement systems?
Customers increasingly prioritise sustainability in their manufacturing processes, with many experiencing climate change’s disruptive effects. Dürr develops cutting-edge systems to efficiently manage exhaust gases and residues, reduce energy consumption, and ensure process reliability. We also design and manufacture industrial silencers for noise control and advanced air filtration solutions to meet the most demanding industrial applications. Dürr’s comprehensive offerings cover all phases, from planning and implementation to ongoing service, delivering exceptional quality and reliability.
With evolving trends in sustainability and efficiency, what is Dürr’s vision for the future of manufacturing? How is the company preparing to meet new challenges and leverage opportunities?
At Dürr, we prioritise integrating innovative technologies such as data analytics, artificial intelligence, energy-saving methods, and waste reduction into our solutions. This ensures sustainability and high efficiency, enabling us to deliver world class manufacturing solutions tailored to specific customer challenges. One standout innovation is the EcoPaintJet, a technology that allows cars to be painted in two colors fully automatically and without overspray. This method combines Dürr’s expertise in paint application, robotics, and software, completing roof painting in just 120 seconds while saving around 15 square meters of masking film. Dürr also invests heavily in research and development to create more sustainable and efficient products and manufacturing processes. We continuously adapt to evolving customer preferences and regulatory requirements while collaborating closely with partners and suppliers to develop and enhance sustainable solutions.
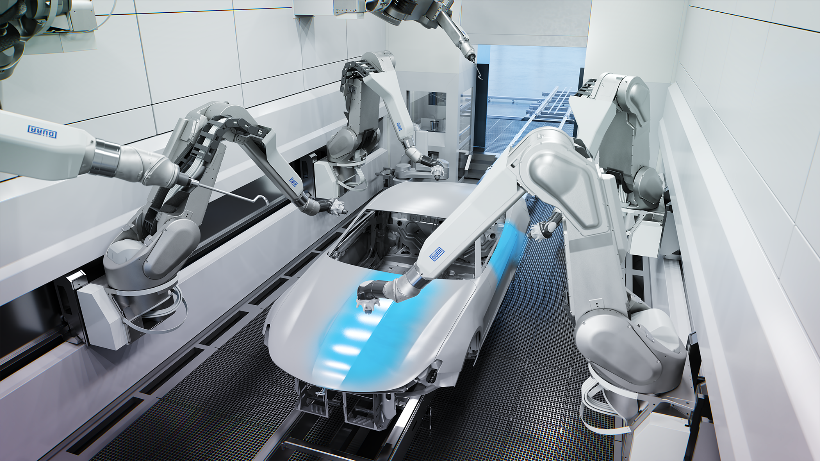
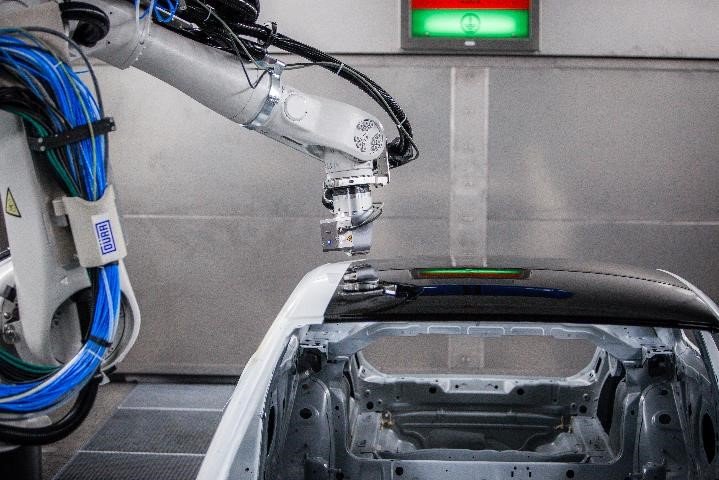