In this article, Jagmeet Singh (VP & Global Head, Digital Engineering Advisory, Cyient) and Leelakishore Haresamudra (Divisional Senior Manager, Cyient) explore the transformative impact of AI-based simulation solvers through a comparative study on cantilever beam analysis. Their findings shed light on the performance, limitations, and business implications of AI in simulation engineering.
Introduction
Simulations in engineering, also known as simulation engineering, involve creating and using computer models and software to represent and analyse the behaviour and performance of real-world systems and phenomena. Simulation engineering can be applied to various domains and industries, such as automotive, aerospace, energy and marine engineering, to test and evaluate various aspects of products and systems, such as design, functionality, safety, and efficiency. Simulation engineering can also be used to explore and optimize various scenarios, parameters, and alternatives, to improve the quality and reliability of the products and systems.
However, simulation engineering also encounters several challenges, including complexity, uncertainty, and scalability, as well as computational and data limitations. As a result, simulation times for complex objects can range from 8–12 hours to 3–4 days. To address these challenges and enhance the capabilities and benefits of simulation engineering, leading simulation software vendors are now leveraging and integrating artificial intelligence (AI).
To gain an in-depth understanding of AI-based simulation solver capabilities, we conducted an AI-based prediction analysis on a simple cantilever beam, focusing solely on structural analysis. In parallel, we also ran simulations using a non-AI-based simulation solver to understand the variation in results.
In this study report, we will discuss the results of this comparison along with the key inferences that are noteworthy from a business adoption perspective.
Experiment Process
The step-by-step process used for conducting the experiment has been outlined in detail. The process consists of the following steps:
- Data Set Up
- Training & Testing of Models
- Predictions
1. Data Set Up
The following data set was developed for the experiment.
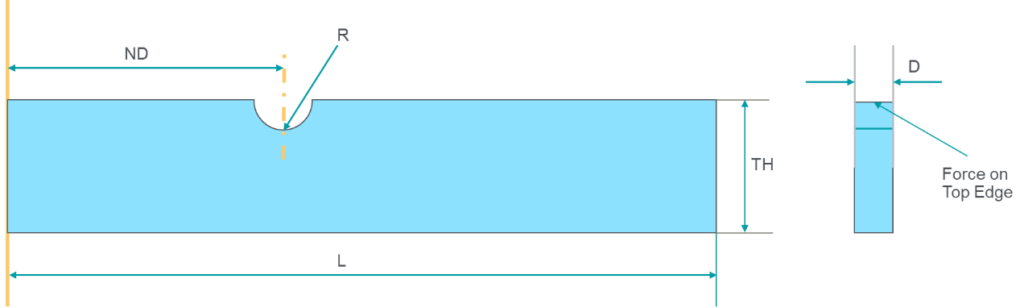
L = Length of the cantilever
R = Notch Radius
D = Depth of the Cantilever
TH = Thickness
ND = Notch Distance from Fixed End
We considered two key variables for the Analysis – Radius (R) and ND (Notch Distance).
With data boundaries and variables established, we initially created a database of 300+ samples for the experiment. Since AI leverages Reduced Order Models (ROMs) to enhance simulation efficiency and accuracy, only 20 models are considered as shown below:
As shown in the sample data set, a range of values has been inserted for Notch Radius and ND along with the resultant displacement for the experiment.
2. Training and Testing of Models
As per the general rule of thumb, 70% of the 20-sample data set was used to train the model and the rest was used for testing. The sample shown below highlights the differences between training and testing data sets.
3. Predictions
We ran the experiment on two different workbenches: one with AI-based solver and the other with a Non-AI-based solver. The results provided great insights, as shown below:
The actual workbench model output is shown to reflect the comparative models.
Key Inferences
- Performance Efficiency: AI based simulation solvers truly add value for designers. They are 10x to 100x faster than non-AI-based simulation solver.
- AI-Driven ROM Generation: AI can leverage machine learning techniques to enhance Reduced Order Models (ROMs) enabling faster simulations and analyses while maintaining accuracy.
- Innovate Faster: AI-based simulation delivers rapid predictions, allowing engineering teams to test more design variations than is possible with traditional solvers.
- Time Savings: These solvers significantly reduce or eliminate the time required to build models, speed up design processes, and lead to better design decisions.
- Workflow Integration: AI-based simulation solvers work directly with meshes or CAD, greatly improving efficiency.
- Predict with Confidence: AI-based simulations include a confidence score that helps detect novel shapes in your data. By evaluating geometric similarity, AI avoids unreliable predictions and ensures accuracy.
- Precision Challenges: AI-based simulation solvers have difficulty accurately calculating discrete quantities.
- Result Variations: The significant variation in results presents challenges for full integration.
Conclusion
Simulation engineering is experiencing significant technological advancements, and business priorities are evolving. According to a McKinsey paper on simulation engineering, there has been a notable shift in business value drivers. Faster time-to-market has become the top priority, replacing product performance, which was previously central to simulation engineering.
Furthermore, while adoption remains relatively low according to McKinsey research, the reasons vary, ranging from technology maturity and accuracy of results to the skill sets required to navigate and understand AI capabilities, among other factors.
In our study, we also observed that AI simulation solvers produced results in considerably less time. However, given that the range of variation was significantly outside industry requirements, these capabilities could not be leveraged in their current form. For example, the aerospace industry can accommodate a variation of only +1% to -1%. This is a strict, non-negotiable rule. In some cases, it may decrease, but it will definitely not increase. Similarly, the automotive industry has specific variation rules for the acceptability and validation of models.
Overall, the responsibility lies with both technology providers and the user community to collaborate and mature the technology for full business integration.