| Industrial automation is no longer just a choice; it is swiftly becoming a requirement to maintain a competitive edge. Let’s discuss how COBOTs can enhance manufacturing and more.
Automation is rapidly and undeniably taking over the manufacturing industry. Manufacturing COBOTs (or collaborative robots) are ideal to fit in the advanced era of automation. With the help of collaborative robots, both large corporations and small businesses can expand and automate processes in their factories, warehouses and research facilities. COBOTs particularly, can perform repetitive, hazardous or precise tasks alongside human workers. Let us look more closely at how COBOTs in manufacturing will undoubtedly play an important role towards the sector’s development. COBOTs are a relatively new aspect of industrial robotics. Because they are simpler, easier and more flexible, COBOTs are designed to be reliable partners that can work hand-in-hand with humans and increase work efficiency and productivity. They pose no risk, require little-to-no programming and simplify connectivity. Because of these benefits, COBOTs are a game changer for a variety of applications. COBOTs are a low-cost, easy-to-use solution that increases productivity while posing fewer risks and providing numerous benefits.
Industrial robots vs COBOTs
In the manufacturing industry, the distinction between COBOTs and robots is based on their intended use and, hence, the type of task assigned to them. Both collaborative robots and industrial robots are used to increase productivity and efficiency by providing more force, energy, accuracy and data. However, reprogramming industrial robots is a complex process which requires a skilled engineer or a developer. COBOTs, on the contrary, are easier to program and quickly learn new skills as they are a fusion of a human and machine which is the most efficient and reliable combination. The following are the differences between Industrial Robots and COBOTs:
• Partnership with humans
A COBOT can double up as an assistant to a human operator. It is designed to work in partnership with humans, while traditional robots are programmed to finish an automated task with little-to-no human interaction.
• Programming
When compared to industrial robots, COBOTs are easier to program. One of the most marketed features of collaborative robots is the ease of programming. COBOTs manufacturing involves user-friendly aspects to aid their application.
• Safety
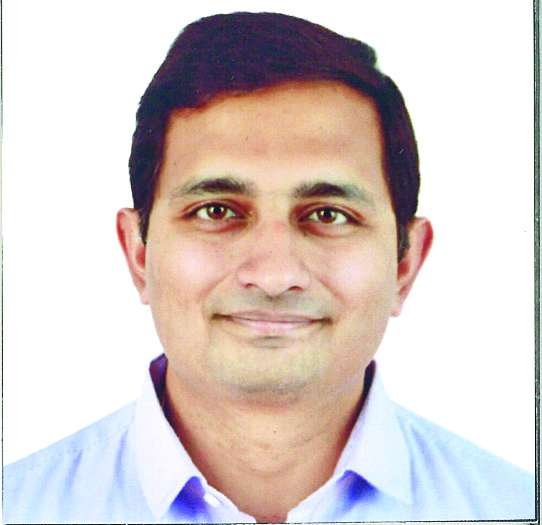
Neelesh Chipade, Head, Product Marketing, Servo, Motion and Robotic Solutions, Mitsubishi Electric India
COBOTs are designed to work alongside people. This means that they are safe enough to function around humans and hence do not need the safety infrastructure that industrial robots require.
• Heavy manufacturing
Industrial robots are capable of handling larger, heavier materials like the ones used in auto manufacturing. Hence, they are well-suited for heavy manufacturing. However, COBOTs are not designed for heavy manufacturing owing to their size and their requirement of working in proximity to human employees.
• Functionality
Traditional industrial robots are usually fixed equipment created for extremely high-precision, volume and speed production. As far as COBOTs are concerned, they are well suited for manufacturers with low volume, high-mix production or those who want to safely automate processes alongside workers. As compared to conventional robots, COBOTs can easily be moved and used in various areas of production. A majority of them can easily be mounted on any surface.Moreover, they are often light-weight and can be carried by a single person.
Benefits of COBOTs in manufacturing
Trained COBOTs can help businesses scale up and automate various production processes, which can lead to consistent working even in the absence of a human for a particular task. The bottom line is that COBOTs in manufacturing can improve quality control, increase
effectiveness and intensify output. They improve the workers’ security by taking control of less desirable or dangerous tasks. COBOTs are generally beneficial to SMEs because they can assist humans efficiently and can prove to be economical for a variety of processes in the long run.
COBOTs’ shortcomings in manufacturing
The disadvantages of COBOTs in manufacturing are not related to their functionality, but rather to the question of whether a particular business should use them or not. For example, as previously stated, COBOTs are not designed fo heavy manufacturing and cannot perform heavy lifting. They are not entirely automated and are always dependent on a human to operate them, which can prove to be an advantage
as well as a disadvantage, depending on their usage. However, there are still some constraints for collaborative robots in terms of cognitive and skilled tasks. Nonetheless, as technology advances, COBOTs — or, more precisely, their engineers and developers — will most likely overcome these. In manufacturing, we can use COBOTs to perform a variety of routine tasks, such as picking and placing; bin-picking;
palletising; packaging; machine maintenance and supervision; testing and quality control; screwing, gluing and sealing and tasks related to the process, such as soldering and welding, sanding, polishing, deburring and grinding. COBOTs are used in a variety of fields and industries due to their adaptabilities, such as the production of goods for the electronics, aerospace, automotive, furniture and plastic modelling industries, to name a few. They also work in agriculture (picking and placing), labs, research, security (monitoring), food services and production (precision tasks, repetitive tasks), healthcare and pharmaceuticals, among other fields.
How the future looks
Expectations as per the various reports state that the COBOT market might show massive growth shortly. COBOTs are quickly becoming a significant component of manufacturing automation as the technology proves to be reliable and more businesses are willing to use it. COBOTs will become more advanced and adaptable over the next few years. Precision and cognitive tasks performed by COBOTs will improve in sync with AI’s capabilities. Furthermore, with the Industrial Internet of Things (IIoT), COBOTs can already connect to other machines, gadgets and network databases. In the future, COBOTs will be able to improve a variety of factory workflows and even offer useful real-time data analytics. Mitsubishi Electric, under its factory automation advancements, has created the collaborative robot ASSISTA.
ASSISTA is an advanced Collaborative Robot that assures security and can work alongside humans. It is simple, easier and more flexible. Furthermore, ASSISTA requires no robot programming expertise, offers immense ease of operation and allows hassle-free connectivity with a wide range of components. ASSISTA epitomises versatility, providing a wide range of components such as Vision, Fingers, Grippers
and other peripherals that are developed by MELFA Robot Partners. These tools allow for easy setup and can easily be configured for specific applications. ASSISTA, can also be configured to move freely either as a mobile robot or as a part of an AGV/AMR. With its adaptable design and simple operation, ASSISTA presents a compelling case as a Collaborative Workspace Partner. Moreover, the operators can easily adjust the robot arm’s position and set waypoints. The six-colour LED ring mounted around the robot’s forearm constantly displays the operational state and fault diagnostics is also notable. ASSISTA, as a Collaborative Workspace Partner, has a lot to offer: flexible design, simple programming, easy use and the ability to connect and work with a variety of components, which is perfect to increase the productivity and efficiency of a human.