| By 2030, nearly one in three vehicles in India will be electric, and one in ten EVs sold worldwide will be in India. However, the Indian EV industry is still in its early stages. Specialised service providers can help them increase the efficiency of their production and reach the next level of technology and collaboration.
Managing Director,
Leadec India
Dr Christoph Jaschinski,
SVP Global Business Development,
Leadec Group
Decreasing battery costs
The costs of a battery system account for the largest share of the manufacturing costs of a vehicle, up to 30–40 percent of total manufacturing costs. This is a challenge for acceptance in India, where, in addition to innovation, the price of the vehicle is the most important purchase criterion. Therefore, all current forecasts show a faster spread of EVs in the two-wheeler segment than in the passenger car segment.
However, with the new process technologies, the manufacturing costs per kWh will decrease during the next few years due to the further development of new materials and their application technologies, irrespective of the location of the plant.
The processes in battery cell production are not yet as industrialised as the assembly processes for ICEs. With new R&D centres in India and Southeast Asia, the manufacturing costs for cells will decrease, which will suit the price sensitivity of Indian customers.
Localise car assembly
Another possibility to reduce costs is to localise car assembly. Today, good imported electric cars are subject to high taxes. As soon as the production is localised, these barriers will become less relevant.
Ramping up production facilities for EVs and even more for cell production will therefore be a crucial factor in the transformation of the automotive industry in India. Major Indian automakers such as Tata Motors, Mahindra & Mahindra, Hyundai Motor India or Maruti have announced significant investments and are trying to make a leap. International manufacturers like Stellantis, Toyota, Audi, BMW, and others are also mulling new facilities for EV manufacturing. In Pune alone, the new Detroit of India, more than 38 EV startups have announced plans to build plants. Among them are companies like Triton, VTRO, Dextro Arts, Tork, and Attron.
Manufacturing efficiency
In order to become cost-efficient against new competitors, Indian car manufacturers will have to reduce their manufacturing costs within the next few years. Reducing the manufacturing costs of a car by 50% means reducing the manufacturing hours by half. Electric cars are mechanically much less complex than cars with internal combustion engines. Companies like Tesla have announced they can produce a car within 10 hours.
More automation, fewer model variants, and new production processes, especially in body construction and final assembly, are the keys to success. In order to maintain cost leadership, particularly in the small and mid-size car segments, Indian automakers will have to rebuild their factories over the next few years in order to remain competitive.
Industrial service companies can provide support along the journey, whether through the engineering and operation of autonomous driving transport systems, the introduction of modular assembly solutions for door trims and other car components, or cloud-based IT applications for products that replace traditional hardware on the lines.
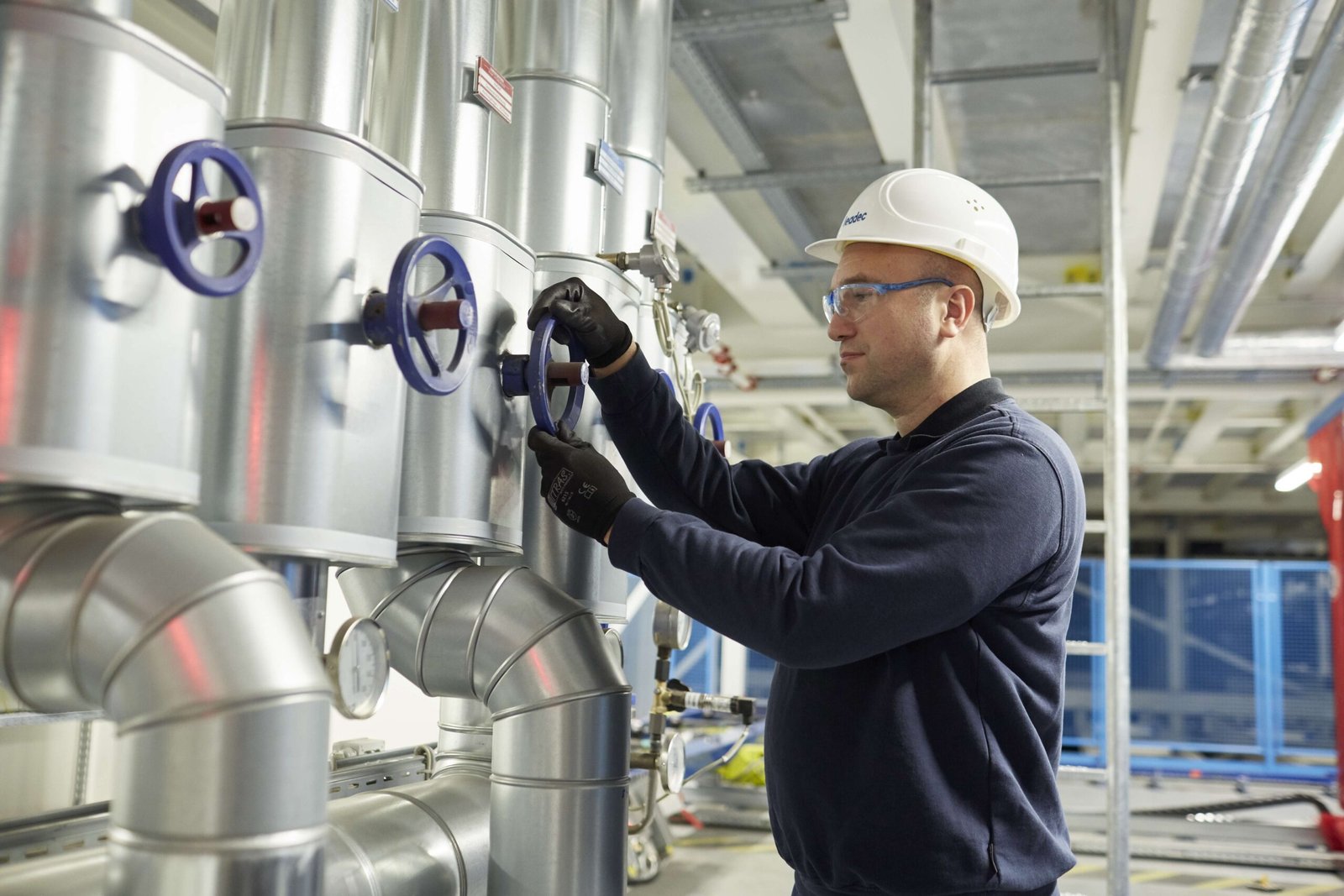
Utilities O&M
Machine Shop
Dr Christoph Jaschinski, SVP Global Business Development, Leadec Group
Sudhir Gurtoo, Managing Director, Leadec India
In EV factories, the following areas are particularly suitable for outsourcing:
- Pre-assembly of batteries and cooling systems.
- Partial assembly of vehicle components such as door panels.
- Maintenance and supply services
- Battery system audits and battery disposal
- Logistics and crating services
- Automation of plant systems
Safety first
Media reports of electric vehicles, especially electric scooters, catching fire in different parts of the country have raised concerns among many people: are EVs really safe? Most electric vehicle manufacturers address the risk of fire and explosion in batteries with efficient and intelligent battery management systems (BMS) that perform the tasks of battery cooling, heating, insulation, ventilation, etc. The certification agencies, the Automotive Research Association of India (ARAI), and the International Centre for Automotive Technology (ICAT) do rigorous testing for overcharge, short circuit, and vibration.
For some new EV companies, the manufacturing processes have been questioned, especially by veterans from the automotive industry. The automotive industry is known for its high standards, and these should also apply to EV production. Trained professionals in the factories are also a must to guarantee safety.
There will be an increasing demand for technical service specialists in SOPs for battery and cooling system assembly as well as for battery repair end-of-line and end-of-life. Moreover, cell and battery production requires new qualifications: Instead of specialists in manufacturing technologies (e.g., welding or assembly), know-how in process technologies (e.g., mixing, dispensing, filling, degassing, and gluing) is now needed.
Battery lifecycle
India will require approximately 800 GWh of batteries by 2030 to attain 30% EV penetration. To meet this rising demand, we need to accelerate plans to manufacture Li-ion cells within the country. Manufacturing batteries is only the first step; we have to keep the complete lifecycle in view from error analysis and repair to disposal and recycling.
So far, recycling plants are still in the pilot stage; rapid industrialization is to be expected. Already in three years, the demand for services for the disassembly of batteries and recycling of materials will increase significantly.
Specialised service companies that are already implementing pilot plants for the dismantling of batteries or solutions for the safe storage and transport of used batteries can make an important contribution to accelerating the vertical integration of the supply chain with their special know-how.
The next level of technology and collaboration
Batteries have made great strides in recent years in terms of their development and cost through a combination of rapid technological progress and scaled-up production rates, but they still need further intelligent development. The focus is on R&D excellence, value chain integration, and flexible manufacturing.
The largest lever is the improvement of cell chemistry and design. One challenge is to further optimise batteries to be able to generate more energy per gram of lithium. New electrode materials also offer the potential to improve performance.
Adapting the manufacturing process holds great potential for cost savings. For example, Tesla uses a single-piece casting design on the Model Y. It not only increase manufacturing efficiency but also increases safety for drivers. Thanks to the casting, the cost of each vehicle’s rear underbody design decreases by 40%.
In order to make rapid progress, new ways of collaboration are also emerging. In May 2022, Volkswagen and Mahindra & Mahindra Ltd. (M&M) announced that they had signed a partnership agreement. Mahindra intends to equip its “Born Electric Platform” with MEB electric components such as electric motors, battery system components, and battery cells from VW. Designed as an open vehicle platform, the MEB electric platform and its components allow car manufacturers to build their portfolio of electrified vehicles, quickly and cost-effectively.
India’s EV Market by 2030
A recent study by Arthur D Little, titled ‘Unlocking India’s Electric mobility potential’ estimates that more than 30 percent of vehicles will be electric by 2030. However, most EVs will be two- and three-wheelers. So, the popular e-rickshaws we see in the North are here to stay and are leading the switch to cleaner transport. Passenger cars will grow slowly, accounting for only five percent of total EV sales.
The driving forces for a transformation of the market will be both the advancement of technology and its adoption by customers. The growing demand continues to pose major challenges for the industry. It starts with the planning and ramp-up of new plants, continues with the transformation of existing plants, moves on to efficient and cost-effective service models, and ends with the supply chain. This is where specialised technical service specialists are needed, with expertise in all aspects of modern factory organisation.
Time to market will be a crucial element for the players. To this end, it is important that they focus on their core competencies and outsource other activities. Manufacturing costs of battery cells and EVs will continue to fall over the next few years. Significant cost components will remain in the form of wage and maintenance costs.
Even though the development of the EV market is promising, one point should not be overlooked: the relocation of production capacities for combustion engine manufacturing to India will still play an important role in the coming years.
Focus on core competencies
Manufacturers have a lot of challenges to meet. Therefore, the transformation to e-mobility also results in an increasing demand for industrial services. Specialists like Leadec now have a special opportunity to contribute their experience from the various waves of automotive product development and support the transformation process. The main areas where industrial service specialists can support automotive manufacturers on their transformation journey are:
- Transformation of existing powertrain plants and industrialization of new technologies, initially in module and pack assembly, later even in cell manufacturing, and vertical integration of the supply chain
- Maintenance and operational support in new technologies, especially from new line builders, are needed to support fast ramp-up and operational excellence
- Automation and operation of the battery module and pack assembly, in-plant battery audit and repair services, and production logistics centres for battery packs
- Manufacturing support services in EV car manufacturing, especially fire protection, hazardous management, onsite battery analytics and repair services, cell handling, and line feeding
- Greenfield support services for new players in the Indian manufacturing market to support time-to-market readiness
Our strategy of an integrated technical services portfolio from engineering to manufacturing support and maintenance services, combined with in-plant logistics and battery repair services, gives key players in the EV industry the opportunity to focus on market introduction and rapid production ramp-up. This allows them to participate disproportionately in the growth of this attractive market and achieve a pole position for future growth.