Jasmino Corporation provides a compelling narrative of its transformation, key technological
contributions, and future growth strategies. Adheesh Ramani, CEO, Jasmino Corporation in
conversation with Anushka Vani highlighted the company’s journey, its commitment to
sustainability, and its strategic focus on global expansion while contributing to India’s “Make in
India” policy.
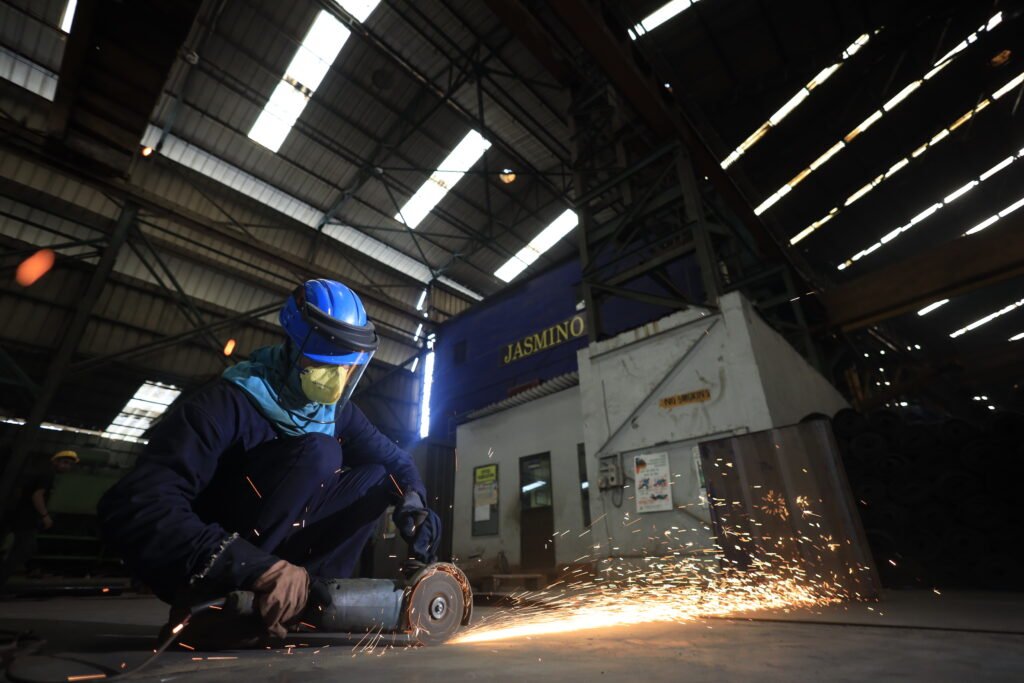
- Can you share the key milestones in Jasmino’s transformation from manufacturing rubber products to becoming a leader in critical equipment protection and anti-corrosive solutions?
Jasmino began in 1978 as a rubber manufacturing company producing molded and extruded rubber products. In 1982, under the leadership of Mr. Ramani Seshadri, our current chairman, who studied at the London School of Rubber, Jasmino expanded into rubber-based lining systems for corrosion protection.
In 2000, Jasmino Polymertech was established with a facility in Taloja, Maharashtra, offering both equipment manufacturing and anti-corrosion linings under one roof. This unique integrated approach quickly earned Jasmino a reputation as a leading engineering partner across India. From there, the company expanded into a wide range of anti-corrosion linings and coatings, while maintaining its core expertise in rubber lining systems.
The company continued to grow, expanding its facilities to 8,400 sq. meters, investing in state-of-the-art machinery, and achieving ISO 9001, ASME ‘U’ Stamp accreditation and OSHA 14001 certifications. In 2016, with expanding horizons toward international growth, the company began establishing a strong presence in the Middle East and Europe.
Driven by the strategic focus of continuing to offer vertically integrated and comprehensive engineering solutions, today, Jasmino offers tailored solutions from concept to commissioning, covering design and engineering, equipment manufacturing, and anti-corrosive lining protection to the entire range of industrial plants both domestically and globally. - How does Jasmino’s rubber lining solution contribute to cleaner and more sustainable industrial operations, particularly in sectors like thermal power and petrochemical industries?
Rubber linings play an important role across various industrial plants by providing corrosion protection and extending the lifespan of critical equipment. They act as a protective barrier against chemicals, corrosive materials, and high temperatures, making them ideal for some of the most severe chemical and abrasive environments, including exposure to high-concentration acids and alkalis.
Industries like chemical, petrochemical, fertilizer, and thermal power plants rely on rubber linings to withstand tough conditions, protect equipment, and protect their critical industrial equipment from corrosion damage. With a strong history of R&D and innovation, Jasmino’s high quality rubber linings prevent wear and tear, and their durability minimizes the need for frequent replacements which helps save resources and cut waste—benefiting both the environment and costs.
In the particular case of FGD (Flue Gas Desulfurization) plants that are frequently deployed in thermal power plants as a way of cleansing the harmful exhaust gases, the core component of the system is the Absorber or Scrubber, where wet limestone is used to react with and absorb sulfur oxides present in the raw gas after coal combustion. The Absorber is a complex piece of equipment that must be protected against heavy corrosion and erosion, as it is exposed to high levels of acid, alkali, and gaseous attacks, as well as solid slurry particles that can erode the metal.
Rubber linings are applied as abrasion and corrosion-resistant barriers in FGD absorbers and have an exceptionally high capacity to withstand sulphur dioxide, making them the most long-term, cost-effective solution for protecting FGD Absorbers, with a service life of 15 to 20 years. - How is Jasmino positioned to meet the growing demand for FGD units in thermal plants, and what role do you see your company playing in reducing environmental impact?
The use of fossil fuels for power generation, a major contributor to India’s energy sector, has long posed environmental risks due to the emission of harmful gases like sulphur dioxide. To address this, the Government of India implemented stringent policies, and the Supreme Court mandate ordered thermal power plants to make sure they only release clean air into the environment. This created a big opportunity for Jasmino Corporation.
With around 260 thermal power plants in India, each with two or more generating units, all are now required to install Flue Gas Desulfurization (FGD) units to clean emissions before release. This represents a market potential of approximately INR 6,000 crore over the next few years. Jasmino Corporation, with its indigenized technology for corrosion protection in FGD scrubbers, is well-positioned to capture a significant share of this market. Rubber lining offers 15 to 20 years of operation in FGD plants. This long-term durability reduces maintenance needs and minimizes downtime, leading to significant cost savings and improved operational reliability for power plants.
Even after accounting for existing competitors and completed work, there remains a substantial untapped market worth an estimated INR 4,500 crore—offering immense growth potential for Jasmino Corporation. - What challenges and opportunities have you encountered while expanding into the Middle East and European markets?
Europe presents several key opportunities for us. Firstly, the shortage of skilled workers and high manufacturing and service costs allowed us to step in as a reliable and cost-effective supplier. Additionally, our proven credentials and successful work with European clients made it easier for us to expand into other Western and international markets, building on our strong reputation.
The Middle East offers favourable business opportunities characterized by a supportive political and economic landscape, along with open-border policies, making it easier to set up local companies, secure visas for workers, and networking with clients. Given the region’s long-standing business associations with India, is encouraging for Indian companies. Additionally, the region is making substantial investments across sectors beyond oil and gas, including petrochemicals, mining, fertilizers, water treatment, and desalination. With established credibility and acceptance in the region, Jasmino Corporation is uniquely positioned to partner on these large-scale industrial projects, unlocking significant opportunities for growth and collaboration.
One significant challenge we faced was the perception of Indian engineering companies, often viewed as cost-effective alternatives rather than equals. This perception made it difficult to establish trust in the European market. To overcome this, we pursued a joint venture strategy, which allowed us to win several projects and acquire a respected German engineering brand, enhancing our trust and reputation. Cultural differences also posed a challenge, including varying communication styles, business practices and language barriers. However, my experience studying and working in Australia helped navigate these differences effectively, fostering stronger connections with our European clients and enhancing our collaborative efforts.
In the Middle East, local partnerships are crucial due to regulatory challenges and the “Make in Middle East” initiative. Finding the right partners can be difficult, but our long-standing relationship with Al-Suhaimi, one of the region’s largest and most influential industrial family houses, has unlocked access to invaluable opportunities. - How is Jasmino contributing to the “Make in India” policy, and how does this enhance cost-effectiveness and competitiveness?
We have successfully indigenized technology for critical applications like FGD scrubbers, establishing ourselves as India’s sole provider of this essential industrial solution. This move not only enhances our technological autonomy but also strengthens our market position. Furthermore, we are shifting more manufacturing to India, creating numerous jobs domestically. This strategic approach allows us to boost local employment for global exports, significantly enhancing our competitive edge in international markets. Additionally, we strive to maximize our operations and sourcing from India, minimizing foreign exchange costs and ensuring cost-effectiveness. Our commitment to indigenization and job creation reflects our dedication to driving sustainable growth and fostering innovation in the industry. - What recent technological advancements or innovations has Jasmino introduced in the area of equipment protection and lining solutions?
Our R&D team is continuously developing new lining and coating solutions that push the boundaries of what is possible in extreme environments. These systems often serve as more cost-effective alternatives to high alloy steels, which are difficult to manufacture in India and are typically imported. Additionally, we have developed lining systems that can withstand temperatures of up to 250°C and protect against almost any type of chemical attack, ensuring long-term performance in demanding applications. - What are Jasmino’s future growth plans, both in the Indian market and internationally?
In the last four years, our company has achieved a CAGR of over 50%, solidifying our market leadership through comprehensive design, engineering, and manufacturing capabilities. With operations in over 15 countries across Asia, the Middle East, and Europe, we have established partnerships and vendors while integrating operations for better efficiency.
Looking ahead, Saudi Arabia represents a key growth opportunity as the region diversifies beyond oil. Our partnership with Al-Suhaimi Group will facilitate our entry into this market and enable expansion into Jordan, Kuwait, and Bahrain, supported by significant capital investment in an operational facility. We are also targeting Australia’s mining sector with plans to open an office there, while exploring expansion in Southeast Asia, particularly Vietnam and Thailand.
In India, we are positioned as the only qualified vendor by National Thermal Power Corporation (NTPC) to provide rubber lining solutions for Flue Gas Desulfurization (FGD) units, addressing a significant market need and contributing to national environmental goals.
Our established history, strong client relationships, and exclusive FGD capabilities position us well for future growth. We are committed to innovation and sustainability while expanding our leadership in this crucial sector