| Industrial automation mainly aims to reduce the necessity of people in manufacturing processes. This allows production to speed up, increase safety and better utilise their resources and industrial analytics in manufacturing. Let’s look into a detailed overview of how
Dinesh Chand Sharma,
Co-chair, Standards, Regulatory and Legal Working Group
IET Future Tech Panel
Automation Goals for Industries
The Internet of Things (IoT) describes a phenomenon where more and more IoT devices are connected to the Internet. It has deeply penetrated all aspects of our lives, businesses and industries, such as smart homes, smart fridges, meters, cities and industrial manufacturing. The terms “digital manufacturing”, “smart manufacturing”, or “intelligent manufacturing” refer to communication and computing technologies that enable all players in the supply chain, enterprise and shop floor levels to be digitally connected and data analytics-driven, thus achieving intelligent coordination for demand and supply matching, faster time to market, mass customisation and cost benefits. New digital and smart technologies are improving processes within the manufacturing industry, leading to what is being called the ‘fourth Industrial Revolution’ or ‘Industry 4.0’. Industry 4.0 or Manufacturing IoT systems connect the components of a production process in a factory. Their purpose is to enable “smart manufacturing”. In smart factories, cyber-physical systems monitor physical processes and make decentralised decisions. Via their IoT connection, these cyber-physical systems can communicate and cooperate with humans in real time.
Achieving industrial automation is accomplished by fully mapping out the industrial process and understanding sub-process relationships enabling machines to work and automate certain process tasks. Companies that use Industry 4.0 technology can perform 10 times better than their peers by being 10 times more effective, efficient and/or faster. They use, for example, smart devices, connected objects and sensors, cloud and big data analytics. The following are the advantages they pose for manufacturing:
Increased Efficiency and Productivity
It enables improved collaboration and coordination between many systems and processes, which leads to quicker and more effective decisions. It reduces downtime and guarantees that the machines always operate efficiently by enabling businesses to schedule maintenance and repairs before an issue arises.
Improved Decision-making through Data Analysis
Due to the large amount of real-time data collected and analysed, industries can immediately identify and address any issues that arise, which reduces waste and boosts productivity.
Reduced Maintenance Costs and Downtime
IoT-led automation provides remote monitoring and control of equipment, which helps reduce downtime by allowing companies to address problems quickly and remotely. Similarly, the data available helps in maintenance and repairs proactively, ahead of time rather than waiting for a machine to malfunction.
Improved Safety
IoT sensors can also monitor environmental factors like temperature, humidity and gas concentrations and notify operators if anything changes that could be dangerous. They are also able to detect impending machine failures and alert maintenance staff, helping in avoiding accidents and ensure workers’ safety.
Attempts for Standardisation
To promote and ensure the take-up of Smart Manufacturing/Industrial automation, favourable policies, pilots and standardisation are crucial. There are several initiatives around Smart Manufacturing/industry 4.0 in Europe and in the Member States. The objective at the European level is to strengthen the coordination among the various initiatives and to facilitate the deployment of smart manufacturing at a pan-European level, thus improving the competitiveness of the European manufacturing industry both in the Single Market and on a global scale and creating the conditions for the European technology providers to flourish.
In April 2016, the European Commission presented the Digitising European Industry initiative (DEI) as part of the Digital Single Market (DSM) strategy which aims to reinforce the EU’s competitiveness in digital technologies and to ensure that every business in Europe — whichever the sector, wherever located, whatever the size — can fully benefit from digital innovation. The European Commission strategy defines four pillars: digital innovation hubs, a regulatory framework, skills development and digital platforms.
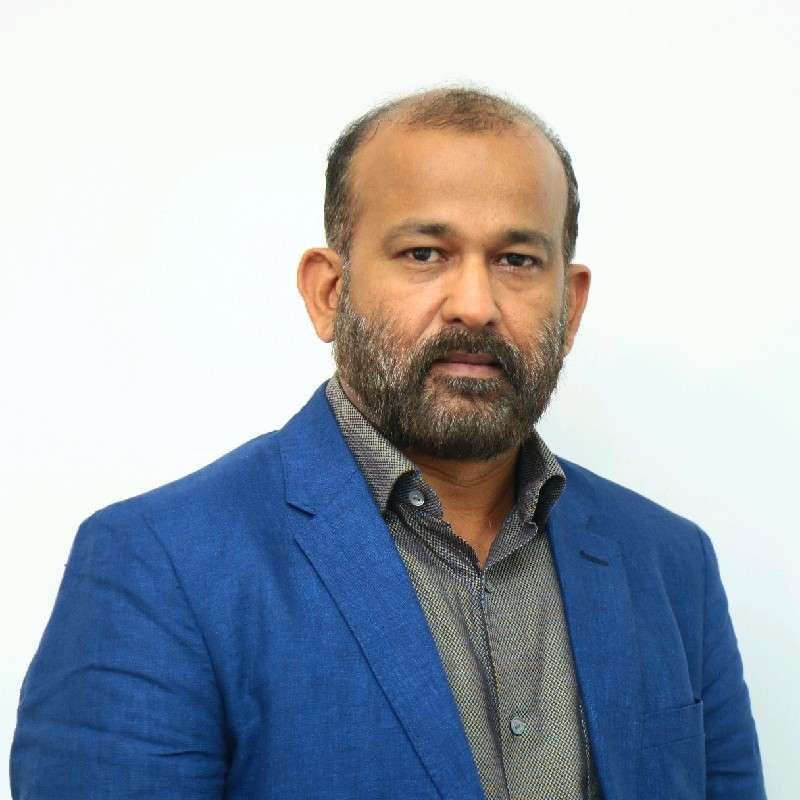
Similarly, to facilitate and create an ecosystem for the propagation of Industry 4.0 set of technologies in every Indian manufacturing by 2025, be it MNC, large, medium or small-scale Indian companies, the “SAMARTH Udyog Bharat 4.0” was launched by the Ministry of Heavy Industries and Public Enterprises, under its scheme on Enhancement of Competitiveness in Indian Capital Goods Sector. SAMARTH Udyog encompasses manufacturers, vendors and customers as the main stakeholders. The initiative aims to raise awareness about Industry 4.0 among the Indian manufacturing industry through demonstration centres. Currently, there are five centres, which include the Centre for Industry 4.0 (C4i4) Lab Pune; IITD-AIA Foundation for Smart Manufacturing; I4.0 India at IISc Factory R & D Platform; Smart Manufacturing Demo & Development Cell at CMTI and Industry 4.0 projects at DHI CoE in Advanced Manufacturing Technology, IIT Kharagpur.
However, the evolution of Smart Manufacturing is still under the microscope and needs more research and development. Standardisation is the other important arm for the creation of a Smart Manufacturing ecosystem that is global, interoperable, secure and safe. Global standards allow devices/equipment to communicate regardless of manufacturer, operating system or other technological details. Currently, these standards are lacking and companies across the globe have been recognising standardisation as the main challenge in implementing Industry 4.0 systems. Some of the key standardisation work carried out for Smart Manufacturing is encapsulated here.
Indian Parameters
In India, the Bureau of Indian Standards (BIS), a National Standard Body, established a technical committee named LITD-34, a Smart Manufacturing Sectional Committee in September 2019, which is responsible for standardisation in the field of Smart Manufacturing including systems-level standardisation. This technical committee is a part of the Electronics and Information Technology Department (LITD) of BIS and mirrors the Systems Committee (SyC) on smart manufacturing at the International Electrotechnical Commission (IEC).
European Parameters
In Europe, standardisation work is being driven forward by various technical committees of CEN/CENELEC and ETSI.
CEN/TC 438: Additive Manufacturing
The main objective of the committee is to standardise the processes of Additive Manufacturing, the test procedures, environmental issues, quality parameters and vocabulary.
CEN/TC 310: Advanced automation technologies and their applications
Standardisation in the field of automation systems and technologies and their application and integration to ensure the availability of the standards required by the industry for design, sourcing, manufacturing and delivery, support, maintenance and disposal of products and their associated services.
CLC/TC 65X: Industrial Process Measurement, Control and Automation
To contribute, support and coordinate the preparation of international standards for systems and elements used for industrial process measurement, control and automation at the CENELEC level. Coordinate standardisation activities which affect the integration of components and functions into such systems including safety and security aspects.
CEN-CENELEC-ETSI: Coordination Group on Smart Manufacturing
The CEN-CENELEC-ETSI Coordination Group on Smart Manufacturing (SMa-CG) was created to coordinate the European standardisation activities relating to new technologies in the field of manufacturing. It is a joint group of CEN, CENELEC and ETSI which advises the CEN-CENELEC Technical Boards and the ETSI Board.
ETSI SmartM2M Technical Committee
This committee has released the SAREF4INMA specification, ETSI TS 103 410-5, to solve the lack of interoperability between various types of production equipment that manufacture items in a factory. It also enables different organisations in the value chain to uniquely track back the manufacturer items for the corresponding production equipment, batches and material and retrieve the exact time of production.
ETSI ISG F5G
This is also addressing the use of fibre for industrial applications to connect with the highest bandwidth and most secure technology for each piece of equipment in industrial production.
Global Parameters
● ISO/TC 184: Automation systems and integration deals with industrial automation technologies, including automated manufacturing equipment, control systems and the supporting information systems, communications and physical interfaces required to integrate them in the world of e-business.
● ISO/TC 261: Additive manufacturing is responsible for Standardisation in the field of Additive Manufacturing (AM) concerning their processes, terms and definitions, process chains (Hardware and Software), test procedures, quality parameters, supply agreements and all kinds of fundamentals.
● IEC System Committee Smart Manufacturing (IEC/SyC): To provide coordination and advice in the domain of Smart Manufacturing to harmonise and advance Smart Manufacturing activities in the IEC, other SDOs and Consortia according to clause 2 in AC/22/2017 superseded by the AC/17/2018.
● IEC/TC 65 is Industrial-process measurement, control and automation: To prepare international standards for systems and elements used for industrial process measurement, control and automation. Coordinate standardisation activities which affect the integration of components and functions into such systems including safety and security aspects. This work of standardisation is to be carried out in the international fields of equipment and systems.
M2M/IoT has opened “never seen before avenues” for manufacturing/Industries to expand their operations in a more scalable, open and integrated manner. In this new industrial future, technology will not replace people, but instead, create new roles and ways of augmenting human qualities and skills. The key would be teaming machines and humans to create effective AIoT, a catalyst of the industrial digital transformation.